Bell Stabilizer Bar System
Arthur M. Young discovered that stability could be increased significantly with the addition of a stabilizer bar perpendicular to the two blades. The stabilizer bar has weighted ends, which cause it to stay relatively stable in the plane of rotation. The stabilizer bar is linked with the swash plate in a manner that reduces the pitch rate. The two blades can flap as a unit and, therefore, do not require lag-lead hinges (the whole rotor slows down and accelerates per turn). Two-bladed systems require a single teetering hinge and two coning hinges to permit modest coning of the rotor disk as thrust is increased. The configuration is known under multiple names, including Hiller panels, Hiller system, Bell-Hiller system, and flybar system.
Offset Flapping Hinge
The offset flapping hinge is offset from the center of the rotor hub and can produce powerful moments useful for controlling the helicopter. The distance of the hinge from the hub (the offset) multiplied by the force produced at the hinge produces a moment at the hub. Obviously, the larger the offset, the greater the moment for the same force produced by the blade.
The flapping motion is the result of the constantly changing balance between lift, centrifugal, and inertial forces. This rising and falling of the blades is characteristic of most helicopters and has often been compared to the beating of a bird’s wing. The flapping hinge, together with the natural flexibility found in most blades, permits the blade to droop considerably when the helicopter is at rest and the rotor is not turning over. During flight, the necessary rigidity is provided by the powerful centrifugal force that results from the rotation of the blades. This force pulls outward from the tip, stiffening the blade, and is the only factor that keeps it from folding up.
Stability Augmentation Systems (SAS)
Some helicopters incorporate stability augmentation systems (SAS) to help stabilize the helicopter in flight and in a hover. The simplest of these systems is a force trim system, which uses a magnetic clutch and springs to hold the cyclic control in the position at which it was released. More advanced systems use electric actuators that make inputs to the hydraulic servos. These servos receive control commands from a computer that senses helicopter attitude. Other inputs, such as heading, speed, altitude, and navigation information may be supplied to the computer to form a complete autopilot system. The SAS may be overridden or disconnected by the pilot at any time. SAS reduces pilot workload by improving basic aircraft control harmony and decreasing disturbances. These systems are very useful when the pilot is required to perform other duties, such as sling loading and search and rescue operations.
Helicopter Vibration
The following paragraphs describe the various types of vibrations. Figure 1 shows the general levels into which frequencies are divided.
 |
Figure 1. Various helicopter vibration types |
Extreme Low Frequency Vibration
Extreme low frequency vibration is pretty well limited to pylon rock. Pylon rocking (two to three cycles per second) is inherent with the rotor, mast, and transmission system. To keep the vibration from reaching noticeable levels, transmission mount dampening is incorporated to absorb the rocking.
Low Frequency Vibration
Low frequency vibrations (1/rev and 2/rev) are caused by the rotor itself. 1/rev vibrations are of two basic types: vertical or lateral. A 1/rev is caused simply by one blade developing more lift at a given point than the other blade develops at the same point.
Medium Frequency Vibration
Medium frequency vibration (4/rev and 6/rev) is another vibration inherent in most rotors. An increase in the level of these vibrations is caused by a change in the capability of the fuselage to absorb vibration, or a loose airframe component, such as the skids, vibrating at that frequency.
High Frequency Vibration
High frequency vibrations can be caused by anything in the helicopter that rotates or vibrates at extremely high speeds. The most common and obvious causes: loose elevator linkage at swashplate horn, loose elevator, or tail rotor balance and track.
Rotor Blade Tracking
Blade tracking is the process of determining the positions of the tips of the rotor blade relative to each other while the rotor head is turning, and of determining the corrections necessary to hold these positions within certain tolerances. The blades should all track one another as closely as possible. The purpose of blade tracking is to bring the tips of all blades into the same tip path throughout their entire cycle of rotation. Various methods of blade tracking are explained in the following paragraphs.
Flag and Pole
The flag and pole method, as shown in Figure 2, shows the relative positions of the rotor blades. The blade tips are marked with chalk or a grease pencil. Each blade tip should be marked with a different color so that it is easy to determine the relationship of the other tips of the rotor blades to each other. This method can be used on all types of helicopters that do not have jet propulsion at the blade tips. Refer to the applicable maintenance manual for specific procedures.
 |
Figure 2. Flag and pole blade tracking |
Electronic Blade Tracker
The most common electronic blade tracker consists of a Balancer/Phazor, Strobex Tracker, and Vibrex Tester. [Figures 3 through 5] The Strobex blade tracker permits blade tracking from inside or outside the helicopter while on the ground or inside the helicopter in flight. The system uses a highly concentrated light beam flashing in sequence with the rotation of the main rotor blades so that a fixed target at the blade tips appears to be stopped. Each blade is identified by an elongated retroreflective number taped or attached to the underside of the blade in a uniform location. When viewed at an angle from inside the helicopter, the taped numbers will appear normal. Tracking can be accomplished with tracking tip cap reflectors and a strobe light. The tip caps are temporarily attached to the tip of each blade. The high-intensity strobe light flashes in time with the rotating blades. The strobe light operates from the aircraft electrical power supply. By observing the reflected tip cap image, it is possible to view the track of the rotating blades. Tracking is accomplished in a sequence of four separate steps: ground tracking, hover verification, forward flight tracking, and auto rotation rpm adjustment.
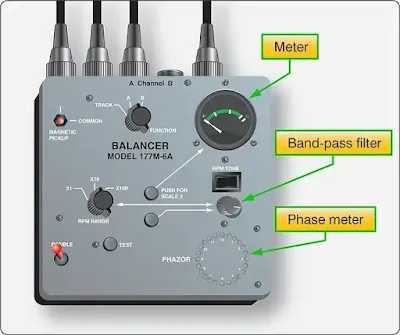 |
Figure 3. Balancer/Phazor |
 |
Figure 4. Strobex tracker |
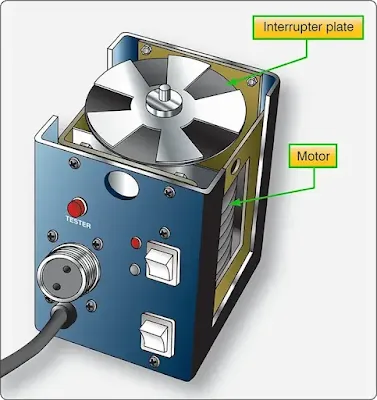 |
Figure 5. Vibrex tracker |
Tail Rotor Tracking
The marking and electronic methods of tail rotor tracking are explained in the following paragraphs.
Marking Method
Procedures for tail rotor tracking using the marking method, as shown in Figure 6, are as follows:
- After replacement or installation of tail rotor hub, blades, or pitch change system, check tail rotor rigging and track tail rotor blades. Tail rotor tip clearance shall be set before tracking and checked again after tracking.
- The strobe-type tracking device may be used if available. Instructions for use are provided with the device. Attach a piece of soft rubber hose six inches long on the end of a ½ × ½ inch pine stick or other flexible device. Cover the rubber hose with Prussian blue or similar type of coloring thinned with oil.
NOTE: Ground run-up shall be performed by authorized personnel only. Start engine in accordance with applicable maintenance manual. Run engine with pedals in neutral position. Reset marking device on underside of tail boom assembly. Slowly move marking device into disk of tail rotor approximately one inch from tip. When near blade is marked, stop engine and allow rotor to stop. Repeat this procedure until tracking mark crosses over to the other blade, then extend pitch control link of unmarked blade one half turn.
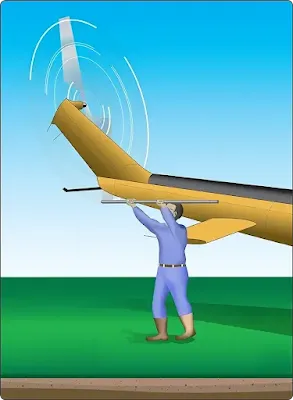 |
Figure 6. Tail rotor tracking |
Electronic Method
The electronic Vibrex balancing and tracking kit is housed in a carrying case and consists of a Model 177M-6A Balancer, a Model 135M-11 Strobex, track and balance charts, an accelerometer, cables, and attaching brackets. The Vibrex balancing kit is used to measure and indicate the level of vibration induced by the main rotor and tail rotor of a helicopter. The Vibrex analyzes the vibration induced by out-of-track or out-of-balance rotors, and then by plotting vibration amplitude and clock angle on a chart the amount and location of rotor track or weight change is determined. In addition, the Vibrex is used in troubleshooting by measuring the vibration levels and frequencies or rpm of unknown disturbances.
Rotor Blade Preservation and Storage
Accomplish the following requirements for rotor blade preservation and storage:
- Condemn, demilitarize, and dispose of locally any blade which has incurred nonrepairable damage.
- Tape all holes in the blade, such as tree damage, or foreign object damage (FOD) to protect the interior of the blade from moisture and corrosion.
- Thoroughly remove foreign matter from the entire exterior surface of blade with mild soap and water.
- Protect blade outboard eroded surfaces with a light coating of corrosion preventive or primer coating.
- Protect blade main bolt hole bushing, drag brace retention bolt hole bushing, and any exposed bare metal (i.e., grip and drag pads) with a light coating of corrosion preventive.
- Secure blade to shock-mounted support and secure container lid.
- Place copy of manufacturer’s blade records, containing information required by Title 14 of the Code of Federal Regulations (14 CFR) section 91.417(a)(2)(ii), and any other blade records in a waterproof bag and insert into container record tube.
- Obliterate old markings from the container that pertained to the original shipment or to the original item it contained. Stencil the blade National Stock Number (NSN), model, and serial number, as applicable, on the outside of the container.
RELATED POSTS