Prepreg and dry fabrics can be cut with hand tools, such as scissors, pizza cutters, and knives. Materials made from Kevlar® are more difficult to cut than fiberglass or carbon and tools wear quicker. A squeegee and a brush are used to impregnate dry fibers with resin for wet layup. Markers, rulers, and circle templates are used to make a repair layout. [Figure 1]
 |
Figure 1. Hand tools for layup |
Air Tools
Air-driven power tools, such as drill motors, routers, and grinders, are used for composite materials. Electric motors are not recommended, because carbon is a conductive material that can cause an electrical short circuit.
If electric tools are used, they need to be of the totally enclosed type. [Figure 2]
 |
Figure 2. Air tools used for composite repair |
Caul Plate
A caul plate made from aluminum is often used to support the part during the cure cycle. A mold release agent, or parting film, is applied to the caul plate so that the part does not attach to the caul plate. A thin caul plate is also used on top of the repair when a heat bonder is used. The caul plate provides a more uniform heated area and it leaves a smoother finish of the composite laminate.
Support Tooling and Molds
Certain repairs require tools to support the part and/or maintain surface contour during cure. A variety of materials can be used to manufacture these tools. The type of material depends on the type of repair, cure temperature, and whether it is a temporary or permanent tool. Support tooling is necessary for oven and autoclave cure due to the high cure temperature. The parts deform if support tooling is not used. There are many types of tooling material available. Some are molded to a specific part contour and others are used as rigid supports to maintain the contour during cure. Plaster is an inexpensive and easy material for contour tooling. It can be filled with fiberglass, hemp, or other material. Plaster is not very durable, but can be used for temporary tools. Often, a layer of fiberglass-reinforced epoxy is placed on the tool side surface to improve the finish quality. Tooling resins are used to impregnate fiberglass, carbon fiber, or other reinforcements to make permanent tools. Complex parts are made from metal or high-temperature tooling boards that are machined with 5-axis CNC equipment to make master tools that can be used to fabricate aircraft parts. [Figures 3 and 4]
 |
Figure 3. Five-axis CNC equipment for tool and mold making |
 |
Figure 4. A mold of an inlet duct |
Vacuum Bag Materials
Repairs of composite aircraft components are often performed with a technique known as vacuum bagging. A plastic bag is sealed around the repair area. Air is then removed from the bag, which allows repair plies to be drawn together with no air trapped in between. Atmospheric pressure bears on the repair and a strong, secure bond is created.
Several processing materials are used for vacuum bagging a part. These materials do not become part of the repair and are discarded after the repair process.
Release Agents
Release agents, also called mold release agents, are used so that the part comes off the tool or caul plate easily after curing.
Bleeder Ply
The bleeder ply creates a path for the air and volatiles to escape from the repair. Excess resin is collected in the bleeder. Bleeder material could be made of a layer of fiberglass, nonwoven polyester, or it could be a perforated Teflon® coated material. The structural repair manual (SRM) indicates what type and how many plies of bleeder are required. As a general rule, the thicker the laminate, the more bleeder plies are required.
Peel Ply
Peel plies are often used to create a clean surface for bonding purposes. A thin layer of fiberglass is cured with the repair part. Just before the part is bonded to another structure, the peel ply is removed. The peel ply is easy to remove and leaves a clean surface for bonding. Peel plies are manufactured from polyester, nylon, flouronated ethylene propylene (FEP), or coated fiberglass. They can be difficult to remove if overheated. Some coated peel plies can leave an undesirable contamination on the surface. The preferred peel ply material is polyester that has been heat-set to eliminate shrinkage.
Layup Tapes
Vacuum bag sealing tape, also called sticky tape, is used to seal the vacuum bag to the part or tool. Always check the temperature rating of the tape before use to ensure that you use appropriately rated tape.
Perforated Release FilmPerforated parting film is used to allow air and volatiles out of the repair, and it prevents the bleeder ply from sticking to the part or repair. It is available with different size holes and hole spacing depending on the amount of bleeding required.
Solid Release Film
Solid release films are used so that the prepreg or wet layup plies do not stick to the working surface or caul plate. Solid release film is also used to prevent the resins from bleeding through and damaging the heat blanket or caul plate if they are used.
Breather Material
The breather material is used to provide a path for air to get out of the vacuum bag. The breather must contact the bleeder. Typically, polyester is used in either 4-ounce or 10-ounce weights. Four ounces is used for applications below 50 pounds per square inch (psi) and 10 ounces is used for 50–100 psi.
Vacuum Bag
The vacuum bag material provides a tough layer between the repair and the atmosphere. The vacuum bag material is available in different temperature ratings, so make sure that the material used for the repair can handle the cure temperature. Most vacuum bag materials are one time use, but material made from flexible silicon rubber is reusable. Two small cuts are made in the bagging material so that the vacuum probe valve can be installed. The vacuum bag is not very flexible and plies need to be made in the bag if complex shapes are to be bagged. Sometimes, an envelope type bag is used, but the disadvantage of this method is that the vacuum pressure might crush the part. Reusable bags made from silicon rubber are available that are more flexible. Some have a built-in heater blanket that simplifies the bagging task. [Figures 5, 6, and 7]
 |
Figure 5. Bagging materials |
 |
Figure 6. Bagging of complex part |
 |
Figure 7. Self-sealing vacuum bag with heater element |
Vacuum Equipment
A vacuum pump is used to evacuate air and volatiles from the vacuum bag so that atmospheric pressure consolidates the plies. A dedicated vacuum pump is used in a repair shop. For repairs on the aircraft, a mobile vacuum pump could be used. Most heat bonders have a built-in vacuum pump. Special air hoses are used as vacuum lines, because regular air hoses might collapse when a vacuum is applied. The vacuum lines that are used in the oven or autoclave need to be able to withstand the high temperatures in the heating device. A vacuum pressure regulator is sometimes used to lower the vacuum pressure during the bagging process.
Vacuum Compaction Table
A vacuum compaction table is a convenient tool for debulking composite layups with multiple plies. Essentially a reusable vacuum bag, a compaction table consists of a metal table surface with a hinged cover. The cover includes a solid frame, a flexible membrane, and a vacuum seal. Repair plies are laid up on the table surface and sealed beneath the cover with vacuum to remove entrapped air. Some compaction tables are heated but most are not.
Heat Sources
Oven
Composite materials can be cured in ovens using various pressure application methods. [Figure 8] Typically, vacuum bagging is used to remove volatiles and trapped air and utilizes atmospheric pressure for consolidation. Another method of pressure application for oven cures is the use of shrink wrapping or shrink tape. The oven uses heated air circulated at high speed to cure the material system. Typical oven cure temperatures are 250 °F and 350 °F. Ovens have a temperature sensor to feed temperature data back to the oven controller. The oven temperature can differ from the actual part temperature depending upon the location of the oven sensor and the location of the part in the oven. The thermal mass of the part in the oven is generally greater than the surrounding oven and during rise to temperature, the part temperature can lag the oven temperature by a considerable amount. To deal with these differences, at least two thermocouples must be placed on the part and connected to a temperature-sensing device (separate chart recorder, hot bonder, etc.) located outside the oven. Some oven controllers can be controlled by thermocouples placed on the repair part.
 |
Figure 8. Walk-in curing oven |
Autoclave
An autoclave system allows a complex chemical reaction to occur inside a pressure vessel according to a specified time, temperature, and pressure profile in order to process a variety of materials. [Figure 9] The evolution of materials and processes has taken autoclave operating conditions from 120 °C (250 °F) and 275 kPa (40 psi) to well over 760 °C (1,400 °F) and 69,000 kPa (10,000 psi). Autoclaves that are operated at lower temperatures and pressures can be pressurized by air, but if higher temperatures and pressures are required for the cure cycle, a 50/50 mixture of air and nitrogen or 100 percent nitrogen should be used to reduce the change of an autoclave fire.
 |
Figure 9. Autoclave |
The major elements of an autoclave system are a vessel to contain pressure, sources to heat the gas stream and circulate it uniformly within the vessel, a subsystem to apply vacuum to parts covered by a vacuum bag, a subsystem to control operating parameters, and a subsystem to load the molds into the autoclave. Modern autoclaves are computer controlled and the operator can write and monitor all types of cure cycle programs. The most accurate way to control the cure cycle is to control the autoclave controller with thermocouples that are placed on the actual part.
Most parts processed in autoclaves are covered with a vacuum bag that is used primarily for compaction of laminates and to provide a path for removal of volatiles. The bag allows the part to be subjected to differential pressure in the autoclave without being directly exposed to the autoclave atmosphere. The vacuum bag is also used to apply varying levels of vacuum to the part.
Heat Bonder and Heat Lamps
Typical on-aircraft heating methods include electrical resistance heat blankets, infrared heat lamps, and hot air devices. All heating devices must be controlled by some means so that the correct amount of heat can be applied. This is particularly important for repairs using prepreg material and adhesives, because controlled heating and cooling rates are usually prescribed.
Heat Bonder
A heat bonder is a portable device that automatically controls heating based on temperature feedback from the repair area. Heat bonders also have a vacuum pump that supplies and monitors the vacuum in the vacuum bag. The heat bonder controls the cure cycle with thermocouples that are placed near the repair. Some repairs require up to 10 thermocouples. Modern heat bonders can run many different types of cure programs and cure cycle data can be printed out or uploaded to a computer. [Figure 10]
 |
Figure 10. Heat bonder equipment |
Heat Blanket
A heat blanket is a flexible heater. It is made of two layers of silicon rubber with a metal resistance heater between the two layers of silicon. Heat blankets are a common method of applying heat for repairs on the aircraft. Heat blankets may be controlled manually; however, they are usually used in conjunction with a heat bonder. Heat is transferred from the blanket via conduction. Consequently, the heat blanket must conform to and be in 100 percent contact with the part, which is usually accomplished using vacuum bag pressure. [Figure 11]
 |
Figure 11. Heat blankets |
Heat Lamp
Infrared heat lamps can also be used for elevated temperature curing of composites if a vacuum bag is not utilized. However, they are generally not effective for producing curing temperatures above 150 °F, or for areas larger than two square feet. It is also difficult to control the heat applied with a lamp, and lamps tend to generate high-surface temperatures quickly. If controlled by thermostats, heat lamps can be useful in applying curing heat to large or irregular surfaces. Heat bonders can be used to control heat lamps.
Hot Air System
Hot air systems can be used to cure composite repairs, and are mainly restricted to small repairs and for drying the repair area. A heat generator supplies hot air that is directed into an insulated enclosure set up around the repair area after vacuum bagging has been deployed. The hot air surrounds the repair for even temperature rise.
Heat Press Forming
During the press forming process, flat stacked thermoplastic prepreg is heated to above melt temperature (340–430 °C, or 645–805 °F) in an oven, rapidly (1–10 seconds) shuttled to a forming die, pressed to shape, and consolidated and cooled under pressure (700–7,000 kPa, or 100–1,000 psi). [Figure 12] In production, press forming dies usually are matched male-female sets constructed of steel or aluminum.
 |
Figure 12. Heat press |
However, rubber, wood, phenolics, and so on can be used during prototyping. The die set can be maintained at room temperature throughout the forming-consolidation cycle. But, the use of a hot die (120–200 °C, or 250–390 °F) allows control of the cooling-down rate (avoiding part warpage and controlling morphology in semicrystalline thermoplastic prepreg, such as PEEK and polyphenylene sulfide) and extends the forming window promoting better ply slip.
The main disadvantage with this method is that the press only applies pressure in one direction, and hence, it is difficult to make complex-shaped (e.g., beads, closed corners) parts or parts with legs that approach vertical. Since the temperature of the die set need not be cycled with each part, rapid forming times of between 10 minutes and 2 hours are achievable with press forming.
Thermocouples
A thermocouple (TC) is a thermoelectric device used to accurately measure temperatures. It may be connected to a simple temperature reading device, or connected to a hot bonder, oven, or other type of controller that regulates the amount of heat. TCs consist of a wire with two leads of dissimilar metals that are joined at one end. Heating the joint produces an electric current, which is converted to a temperature reading with a TC monitor. Select the type of wire (J or K) and the type of connector that are compatible with the local temperature monitoring equipment (hot bonder, oven, autoclave, etc.). TC wire is available with different types of insulation; check the manufacturer’s product data sheets to ensure the insulation withstands the highest cure temperature. Teflon-insulated wire is generally good for 390 °F and lower cures; Kapton-insulated wire should be used for higher temperatures.
Thermocouple Placement
Thermocouple placement is the key in obtaining proper cure temperatures throughout the repair. In general, the thermocouples used for temperature control should be placed as close as possible to the repair material without causing it to become embedded in the repair or producing indentations in the repair. They should also be placed in strategic hot or cold locations to ensure the materials are adequately cured but not exposed to excessively high temperatures that could degrade the material structural properties. The thermocouples should be placed as close as practical to the area that needs to be monitored. The following steps should be taken when using thermocouples:
- Never use fewer than three thermocouples to monitor a heating cycle.
- If bonding a precured patch, place the thermocouple near the center of the patch.
- A control thermocouple may be centered over a low-temperature (200 °F or lower) co-cured patch as long as it is placed on top of a thin metallic sheet to prevent a thermocouple indentation onto the patch. This may allow for a more accurate control of the patch temperature.
- The thermocouples installed around the perimeter of the repair patch should be placed approximately 0.5‑inch away from the edge of the adhesive line.
- Place flash tape below and above the thermocouple tips to protect them from resin flash and to protect the control unit from electrical shorts.
- Do not place the thermocouple under the vacuum port as the pressure may damage the lead and cause erroneous readings to occur.
- Do not place thermocouple wires adjacent to or crossing the heat blanket power cord to prevent erroneous temperature readings caused by magnetic flux lines.
- Do not place any control thermocouple beyond the heat blanket’s two-inch overlap of the repair to prevent the controller from trying to compensate for the lower temperature.
- Always leave slack in the thermocouple wire under the vacuum bag to prevent the thermocouple from being pulled away from the area to be monitored as vacuum is applied.
Thermal Survey of Repair Area
In order to achieve maximum structural bonded composite repair, it is essential to cure these materials within the recommended temperature range. Failure to cure at the correct temperatures can produce weak patches and/or bonding surfaces and can result in a repair failure during service. A thermal survey should be performed prior to installing the repair to ensure proper and uniform temperatures can be achieved. The thermal survey determines the heating and insulation requirements, as well as TC locations for the repair area. The thermal survey is especially useful for determining the methods of heating (hot air modules, heat lamps, heat blanket method and monitoring requirements in cases where heat sinks (substructure for instance) exist in the repair area). It should be performed for all types of heating methods to preclude insufficient, excessive, or uneven heating of the repair area.
Temperature Variations in Repair Zone
Thermal variations in the repair area occur for many reasons. Primary among these are material type, material thickness, and underlying structure in the repair zone. For these reasons, it is important to know the structural composition of the area to be repaired. Substructure existing in the repair zone conducts heat away from the repair area, resulting in a cold spot directly above the structure. Thin skins heat quickly and can easily be overheated. Thick skin sections absorb heat slowly and take longer to reach soak temperature. The thermal survey identifies these problem areas and allows the technician to develop the heat and insulation setup required for even heating of the repair area.
Thermal Survey
During the thermal survey process, try to determine possible hot and cold areas in the repair zone. Temporarily attach a patch of the same material and thickness, several thermal couples, heating blanket, and a vacuum bag to the repair area. Heat the area and, after the temperature is stabilized, record the thermocouple temperatures. Add insulation if the temperature of the thermocouple varies more than 10 degrees from average. The areas with a stringer and rib indicate a lower temperature than the middle of the patch because they act as a heat sink. Add insulation to these areas to increase the temperature. [Figure 13]
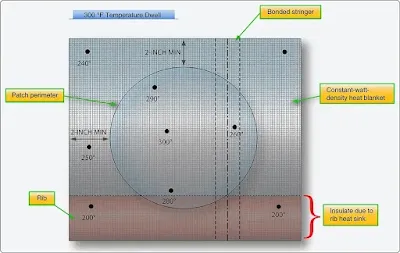 |
Figure 13. Thermal survey example |
Solutions to Heat Sink Problems
Additional insulation can be placed over the repair area. This insulation can also be extended beyond the repair area to minimize heat being conducted away. Breather materials and fiberglass cloths work well, either on top of the vacuum bag or within the vacuum bag or on the accessible backside of the structure. Place more insulation over cool spots and less insulation over hot spots. If access is available to the backside of the repair area, additional heat blankets could be placed there to heat the repair area more evenly.
RELATED POSTS