Oxy-Acetylene or Oxygen Acetylene welding is a type of welding that relies on the combustion of oxygen and acetylene gases, hence often referred to as gas welding. It is one of the most versatile types of welding. Oxy-Acetylene welding requires a specific skill set and thorough practice, coupled with which it can be used to weld virtually any metal. Oxy-Acetylene welding works on a simple concept, that is, bring two pieces of metals together such that their edges are touching. Then, heat these touching edges with a flame till they melt and fuse. Figure 1 shows various types of basic joints.
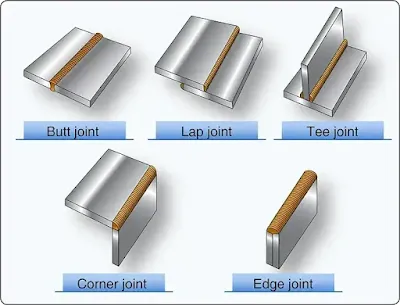 |
Figure 1. Basic joints |
Butt Joints
A butt joint is made by placing two pieces of material edge to edge, without overlap, and then welding. A plain butt joint is used for metals from 1⁄16-inch to 1⁄8-inch in thickness. A filler rod is used when making this joint to obtain a strong weld.
The flanged butt joint can be used in welding thin sheets, 1⁄16- inch or less. The edges are prepared for welding by turning up a flange equal to the thickness of the metal. This type of joint is usually made without the use of a filler rod.
If the metal is thicker than 1⁄8-inch, it may be necessary to bevel the edges so that the heat from the torch can completely penetrate the metal. These bevels may be either single or double-bevel type or single or double-V type. A filler rod is used to add strength and reinforcement to the weld. [Figure 2]
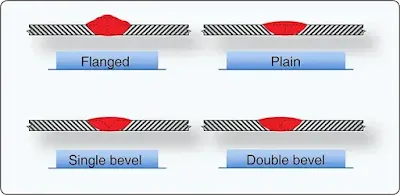 |
Figure 2. Types of butt joints |
Repair of cracks by welding may be considered just another type of butt joint. The crack should be stop drilled at either end and then welded like a plain butt joint using filler rod. In most cases, the welding of the crack does not constitute a complete repair and some form of reinforcement is still required, as described in following sections.
Tee Joints
A tee joint is formed when the edge or end of one piece is welded to the surface of another. [Figure 3] These joints are quite common in aircraft construction, particularly in tubular structures. The plain tee joint is suitable for most thicknesses of metal used in aircraft, but heavier thicknesses require the vertical member to be either single or double-beveled to permit the heat to penetrate deeply enough.
 |
Figure 3. Types of tee joints showing filler penetration |
The dark areas in Figure 3 show the depth of heat penetration and fusion required. It is a good practice to leave a gap between the parts, about equal to the metal thickness to aid full penetration of the weld. This is common when welding from only one side with tubing clusters. Tight fitment of the parts prior to welding does not provide for a proper weldment unless full penetration is secured, and this is much more difficult with a gapless fitment.
Edge Joints
An edge joint is used when two pieces of sheet metal must be fastened together and load stresses are not important. Edge joints are usually made by bending the edges of one or both parts upward, placing the two ends parallel to each other, and welding along the outside of the seam formed by the two joined edges. The joint shown in Figure 4 requires no filler rod since the edges can be melted down to fill the seam. The joint shown in Figure 4, being thicker material, must be beveled for heat penetration; filler rod is added for reinforcement.
 |
Figure 4. Edge joints |
Corner Joints
A corner joint is made when two pieces of metal are brought together so that their edges form a corner of a box or enclosure. [Figure 5] The corner joint shown in Figure 5A requires no filler rod, since the edges fuse to make the weld. It is used where the load stress is not important.
 |
Figure 5. Corner joints |
The type shown in Figure 5B is used on heavier metals, and filler rod is added for roundness and strength. If a higher stress is to be placed on the corner, the inside is reinforced with another weld bead. [Figure 5C]
Lap Joints
The lap joint is seldom used in aircraft structures when welding with oxy-acetylene, but is commonly used and joined by spot welding. The single lap joint has very little resistance to bending, and cannot withstand the shearing stress to which the weld may be subjected under tension or compression loads. The double lap joint offers more strength, but requires twice the amount of welding required on the simpler, more efficient butt weld. [Figure 6]
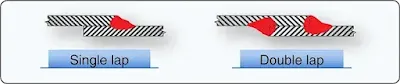 |
Figure 6. Single and double lap joints |
RELATE POSTS