Flow control valves control the speed and/or direction of fluid flow in the hydraulic system. They provide for the operation of various components when desired and the speed at which the component operates. Examples of flow control valves include: selector valves, check valves, sequence valves, priority valves, shuttle valves, quick disconnect valves, and hydraulic fuses.
A selector valve is used to control the direction of movement of a hydraulic actuating cylinder or similar device. It provides for the simultaneous flow of hydraulic fluid both into and out of the unit. Hydraulic system pressure can be routed with the selector valve to operate the unit in either direction and a corresponding return path for the fluid to the reservoir is provided.
Selector valves may be poppet-type, spool-type, piston-type, rotary-type, or plug-type. [Figure 2] Regardless, each selector valve has a unique number of ports. The number of ports is determined by the particular requirements of the system in which the valve is used. Closed-centered selector valves with four ports are most common in aircraft hydraulic systems. These are known as four-way valves. Figure 1 illustrates how this valve connects to the pressure and return lines of the hydraulic system, as well as to the two ports on a common actuator. Most selector valves are mechanically controlled by a lever or electrically controlled by solenoid or servo. [Figure 3]
 |
Figure 2. A poppet-type four-way selector valve |
 |
Figure 3. Four-way servo control valve |
The four ports on a four-way selector valve always have the same function. One port receives pressurized fluid from the system hydraulic pump. A second port always returns fluid to the reservoir. The third and forth ports are used to connect the selector valve to the actuating unit. There are two ports on the actuating unit. When the selector valve is positioned to connect pressure to one port on the actuator, the other actuator port is simultaneously connected to the reservoir return line through selector valve. [Figure 1-B] Thus, the unit operates in a certain direction. When the selector valve is positioned to connect pressure to the other port on the actuating unit, the original port is simultaneously connected to the return line through the selector valve and the unit operates in the opposite direction. [Figure 1-C]
Figure 4 illustrates the internal flow paths of a solenoid operated selector valve. The closed center valve is shown in the NEUTRAL or OFF position. Neither solenoid is energized. The pressure port routes fluid to the center lobe on the spool, which blocks the flow. Fluid pressure flows through the pilot valves and applies equal pressure on both ends of the spool. The actuator lines are connected around the spool to the return line.
 |
Figure 4. Servo control valve solenoids not energized |
When selected via a switch in the cockpit, the right solenoid is energized. The right pilot valve plug shifts left, which blocks pressurized fluid from reaching the right end of the main spool. The spool slides to the right due to greater pressure applied on the left end of the spool. The center lobe of the spool no longer blocks system pressurized fluid, which flows to the actuator through the left actuator line. At the same time, return flow is blocked from the main spool left chamber so the actuator (not shown) moves in the selected direction. Return fluid from the moving actuator flows through the right actuator line past the spool and into the return line. [Figure 5]
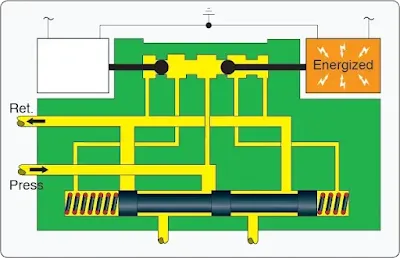 |
Figure 5. Servo control valve right solenoid energized |
Typically, the actuator or moving device contacts a limit switch when the desired motion is complete. The switch causes the right solenoid to de-energize and the right pilot valve reopens. Pressurized fluid can once again flow through the pilot valve and into the main spool right end chamber. There, the spring and fluid pressure shift the spool back to the left into the NEUTRAL or OFF position shown in Figure 4.
To make the actuator move in the opposite direction, the cockpit switch is moved in the opposite direction. All motion inside the selector valve is the same as described above but in the opposite direction. The left solenoid is energized. Pressure is applied to the actuator through the right port and return fluid from the left actuator line is connected to the return port through the motion of the spool to the left.
Check Valve
Another common flow control valve in aircraft hydraulic systems is the check valve. A check valve allows fluid to flow unimpeded in one direction, but prevents or restricts fluid flow in the opposite direction. A check valve may be an independent component situated in-line somewhere in the hydraulic system or it may be built-in to a component. When part of a component, the check valve is said to be an integral check valve.
A typical check valve consists of a spring loaded ball and seat inside a housing. The spring compresses to allow fluid flow in the designed direction. When flow stops, the spring pushes the ball against the seat which prevents fluid from flowing in the opposite direction through the valve. An arrow on the outside of the housing indicated the direction in which fluid flow is permitted. [Figure 6] A check valve may also be constructed with spring loaded flapper or coned shape piston instead of a ball.
 |
Figure 6. An in-line check valve and orifice type in-line check valve |
Orifice-Type Check Valve
Some check valves allow full fluid flow in one direction and restricted flow in the opposite direction. These are known as orifice-type check valves, or damping valves. The valve contains the same spring, ball, and seat combination as a normal check valve but the seat area has a calibrated orifice machined into it. Thus fluid flow is unrestricted in the designed direction while the ball is pushed off of its seat. The downstream actuator operates at full speed. When fluid back flows into the valve, the spring forces the ball against the seat which limits fluid flow to the amount that can pass through the orifice. The reduced flow in this opposite direction slows the motion, or dampens, the actuator associated with the check valve. [Figure 6]
An orifice check valve may be included in a hydraulic landing gear actuator system. When the gear is raised, the check valve allows full fluid flow to lift the heavy gear at maximum speed. When lowering the gear, the orifice in the check valve prevents the gear from violently dropping by restricting fluid flow out of the actuating cylinder.
Sequence Valves
Sequence valves control the sequence of operation between two branches in a circuit; they enable one unit to automatically set another unit into motion. An example of the use of a sequence valve is in an aircraft landing gear actuating system. In a landing gear actuating system, the landing gear doors must open before the landing gear starts to extend. Conversely, the landing gear must be completely retracted before the doors close. A sequence valve installed in each landing gear actuating line performs this function. A sequence valve is somewhat similar to a relief valve except that, after the set pressure has been reached, the sequence valve diverts the fluid to a second actuator or motor to do work in another part of the system. There are various types of sequence valves. Some are controlled by pressure, some are controlled mechanically, and some are controlled by electric switches.
Pressure-Controlled Sequence Valve
The operation of a typical pressure-controlled sequence valve is illustrated in Figure 4. The opening pressure is obtained by adjusting the tension of the spring that normally holds the piston in the closed position. (Note that the top part of the piston has a larger diameter than the lower part.) Fluid enters the valve through the inlet port, flows around the lower part of the piston and exits the outlet port, where it flows to the primary (first) unit to be operated. [Figure 7-A] This fluid pressure also acts against the lower surface of the piston.
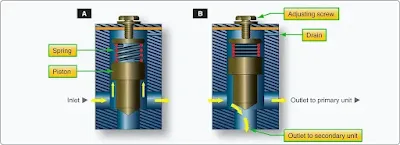 |
Figure 7. A pressure-controlled sequence valve |
When the primary actuating unit completes its operation, pressure in the line to the actuating unit increases sufficiently to overcome the force of the spring, and the piston rises. The valve is then in the open position. [Figure 7-B] The fluid entering the valve takes the path of least resistance and flows to the secondary unit. A drain passage is provided to allow any fluid leaking past the piston to flow from the top of the valve. In hydraulic systems, this drain line is usually connected to the main return line.
Mechanically Operated Sequence Valve
The mechanically operated sequence valve is operated by a plunger that extends through the body of the valve. [Figure 8] The valve is mounted so that the plunger is operated by the primary unit. A check valve, either a ball or a poppet, is installed between the fluid ports in the body. It can be unseated by either the plunger or fluid pressure. Port A and the actuator of the primary unit are connected by a common line. Port B is connected by a line to the actuator of the secondary unit. When fluid under pressure flows to the primary unit, it also flows into the sequence valve through port A to the seated check valve in the sequence valve. In order to operate the secondary unit, the fluid must flow through the sequence valve. The valve is located so that the primary unit moves the plunger as it completes its operation. The plunger unseats the check valve and allows the fluid to flow through the valve, out port B, and to the secondary unit.
 |
Figure 8. Mechanically operated sequence valve |
Priority Valves
A priority valve gives priority to the critical hydraulic subsystems over noncritical systems when system pressure is low. For instance, if the pressure of the priority valve is set for 2,200 psi, all systems receive pressure when the pressure is above 2,200 psi. If the pressure drops below 2,200 psi, the priority valve closes and no fluid pressure flows to the noncritical systems. [Figure 9] Some hydraulic designs use pressure switches and electrical shutoff valves to assure that the critical systems have priority over noncritical systems when system pressure is low.
 |
Figure 9. Priority valve |
Quick Disconnect Valves
Quick disconnect valves are installed in hydraulic lines to prevent loss of fluid when units are removed. Such valves are installed in the pressure and suction lines of the system immediately upstream and downstream of the power pump. In addition to pump removal, a power pump can be disconnected from the system and a hydraulic test stand connected in its place. These valve units consist of two interconnecting sections coupled together by a nut when installed in the system. Each valve section has a piston and poppet assembly. These are spring loaded to the closed position when the unit is disconnected. [Figure 10]
 |
Figure 10. A hydraulic quick-disconnect valve |
Hydraulic Fuses
A hydraulic fuse is a safety device. Fuses may be installed at strategic locations throughout a hydraulic system. They detect a sudden increase in flow, such as a burst downstream, and shut off the fluid flow. By closing, a fuse preserves hydraulic fluid for the rest of the system. Hydraulic fuses are fitted to the brake system, leading edge flap and slat extend and retract lines, nose landing gear up and down lines, and the thrust reverser pressure and return lines. One type of fuse, referred to as the automatic resetting type, is designed to allow a certain volume of fluid per minute to pass through it. If the volume passing through the fuse becomes excessive, the fuse closes and shuts off the flow. When the pressure is removed from the pressure supply side of the fuse, it automatically resets itself to the open position. Fuses are usually cylindrical in shape, with an inlet and outlet port at opposite ends. [Figure 11]
 |
Figure 11. Hydraulic fuse |
Pressure Control Valves
The safe and efficient operation of fluid power systems, system components, and related equipment requires a means of controlling pressure. There are many types of automatic pressure control valves. Some of them are an escape for pressure that exceeds a set pressure; some only reduce the pressure to a lower pressure system or subsystem; and some keep the pressure in a system within a required range.
Relief Valves
Hydraulic pressure must be regulated in order to use it to perform the desired tasks. A pressure relief valve is used to limit the amount of pressure being exerted on a confined liquid. This is necessary to prevent failure of components or rupture of hydraulic lines under excessive pressures. The pressure relief valve is, in effect, a system safety valve.
 |
Figure 12. Pressure relief valve |
The design of pressure relief valves incorporates adjustable spring-loaded valves. They are installed in such a manner as to discharge fluid from the pressure line into a reservoir return line when the pressure exceeds the predetermined maximum for which the valve is adjusted. Various makes and designs of pressure relief valves are in use, but, in general, they all employ a spring-loaded valving device operated by hydraulic pressure and spring tension. [Figure 12] Pressure relief valves are adjusted by increasing or decreasing the tension on the spring to determine the pressure required to open the valve. They may be classified by type of construction or uses in the system. The most common types of valve are:
- Ball type-in pressure relief valves with a ball-type valving device, the ball rests on a contoured seat. Pressure acting on the bottom of the ball pushes it off its seat, allowing the fluid to bypass.
- Sleeve type-in pressure relief valves with a sleeve-type valving device, the ball remains stationary and a sleeve-type seat is moved up by the fluid pressure. This allows the fluid to bypass between the ball and the sliding sleeve-type seat.
- Poppet type-in pressure relief valves with a poppet-type valving device, a cone-shaped poppet may have any of several design configurations; however, it is basically a cone and seat machined at matched angles to prevent leakage. As the pressure rises to its predetermined setting, the poppet is lifted off its seat, as in the ball-type device. This allows the fluid to pass through the opening created and out the return port.
Pressure relief valves cannot be used as pressure regulators in large hydraulic systems that depend on engine-driven pumps for the primary source of pressure because the pump is constantly under load and the energy expended in holding the pressure relief valve off its seat is changed into heat. This heat is transferred to the fluid and, in turn, to the packing rings, causing them to deteriorate rapidly. Pressure relief valves, however, may be used as pressure regulators in small, low-pressure systems or when the pump is electrically driven and is used intermittently.
Pressure relief valves may be used as:
- System relief valve—the most common use of the pressure relief valve is as a safety device against the possible failure of a pump compensator or other pressure regulating device. All hydraulic systems that have hydraulic pumps incorporate pressure relief valves as safety devices.
- Thermal relief valve—the pressure relief valve is used to relieve excessive pressures that may exist due to thermal expansion of the fluid. They are used where a check valve or selector valve prevents pressure from being relieved through the main system relief valve. Thermal relief valves are usually smaller than system relief valves. As pressurized fluid in the line in which it is installed builds to an excessive amount, the valve poppet is forced off its seat. This allows excessive pressurized fluid to flow through the relief valve to the reservoir return line. When system pressure decreases to a predetermined pressure, spring tension overcomes system pressure and forces the valve poppet to the closed position.
Pressure Regulators
The term pressure regulator is applied to a device used in hydraulic systems that are pressurized by constant-delivery type pumps. One purpose of the pressure regulator is to manage the output of the pump to maintain system operating pressure within a predetermined range. The other purpose is to permit the pump to turn without resistance (termed unloading the pump) at times when pressure in the system is within normal operating range. The pressure regulator is located in the system so that pump output can get into the system pressure circuit only by passing through the regulator. The combination of a constant-delivery-type pump and the pressure regulator is virtually the equivalent of a compensator-controlled, variable-delivery-type pump. [Figure 13]
 |
Figure 13. The location of a pressure regulator in a basic hydraulic system. The regulator unloads the constant delivery pump by bypassing fluid to the return line when the predetermined system pressure is reached |
Pressure Reducers
Pressure reducing valves are used in hydraulic systems where it is necessary to lower the normal system operating pressure by a specified amount. Pressure reducing valves provide a steady pressure into a system that operates at a lower pressure than the supply system. A reducing valve can normally be set for any desired downstream pressure within the design limits of the valve. Once the valve is set, the reduced pressure is maintained regardless of changes in supply pressure (as long as the supply pressure is at least as high as the reduced pressure desired) and regardless of the system load, if the load does not exceed the designed capacity of the reducer. [Figure 14]
 |
Figure 14. Operating mechanism of a pressure reducing valve |
Shuttle Valves
In certain fluid power systems, the supply of fluid to a subsystem must be from more than one source to meet system requirements. In some systems, an emergency system is provided as a source of pressure in the event of normal system failure. The emergency system usually actuates only essential components. The main purpose of the shuttle valve is to isolate the normal system from an alternate or emergency system. It is small and simple; yet, it is a very important component. [Figure 15] The housing contains three ports—normal system inlet, alternate or emergency system inlet, and outlet. A shuttle valve used to operate more than one actuating unit may contain additional unit outlet ports.
 |
Figure 15. A spring-loaded piston-type shuttle valve in normal configuration (A) and with alternate/emergency supply (B) |
Enclosed in the housing is a sliding part called the shuttle. Its purpose is to seal off one of the inlet ports. There is a shuttle seat at each inlet port. When a shuttle valve is in the normal operation position, fluid has a free flow from the normal system inlet port, through the valve, and out through the outlet port to the actuating unit. The shuttle is seated against the alternate system inlet port and held there by normal system pressure and by the shuttle valve spring. The shuttle remains in this position until the alternate system is activated. This action directs fluid under pressure from the alternate system to the shuttle valve and forces the shuttle from the alternate system inlet port to the normal system inlet port. Fluid from the alternate system then has a free flow to the outlet port, but is prevented from entering the normal system by the shuttle, which seals off the normal system port.
The shuttle may be one of four types:
- Sliding plunge
- Spring-loaded piston
- Spring-loaded ball
- Spring-loaded poppet
In shuttle valves that are designed with a spring, the shuttle is normally held against the alternate system inlet port by the spring.
Shutoff Valves
Shutoff valves are used to shutoff the flow of fluid to a particular system or component. In general, these types of valves are electrically powered. Shutoff valves are also used to create a priority in a hydraulic system and are controlled by pressure switches. [Figure 15]
 |
Figure 15. Shutoff valves |